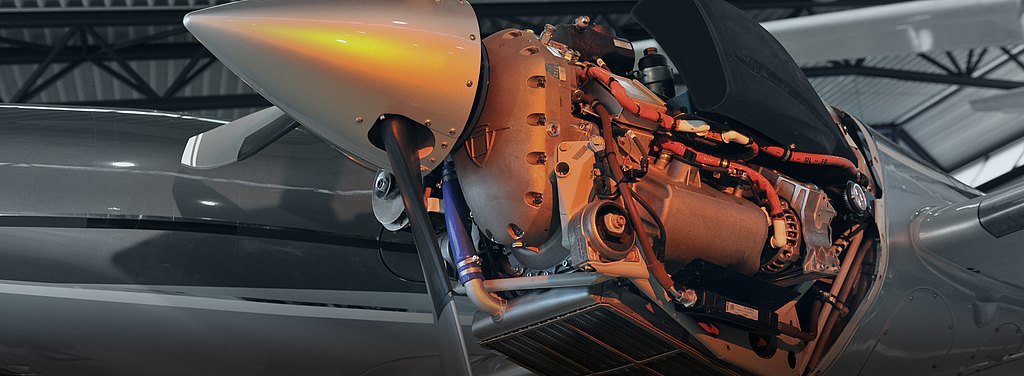
MSB-E4-039
Additional Information
Austro Engine has identified an issue with a limited number of Austro E4 Engines that can be rectified by the applicable Mandatory Service Bulletin (MSB). The information provided on this page is intended to give you an overview of the MSB and is not a substitute of the MSB itself.
MSB-E4-039 What is it about?
The MSB is in relation to the tolerance/fit between the cylinder bore (inside diameter) and the piston (outside diameter), which if it remains unverified could lead to increased wear outside of normal expectations. Further to that, the tolerance/fit between the piston boss (inner shape) and the piston pin boss (outer shape) has also shown some criticalities that likewise could lead to excessive wear. To correct this condition, affected engines are divided into four groups according to the level of geometrical deviation and if they are installed in single- or multi-engine planes.
For more details and instructions refer to
MSB-E4-039
Please find more information about our approach to solve the issue, answers to your frequently asked questions and more background information.
Proactive Approach What's been done?
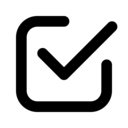
Proactive authorized service centers notification
Two weeks before the bulletin was published, we contacted all our authorized service centers to brief them on the MSB implications and to prepare them to react quickly. The briefing covered the impact of the MSB, how to carry out corrective measures, and what the next steps would be.
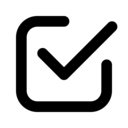
Proactive parts shipment
We started supplying our authorized service centers early and proactively, without waiting for their purchase orders, so they can serve affected customers as quickly as possible. Through internal analysis of the affected engine serial numbers, we made an initial prioritization based on the impact on each customer. Thus, we could fulfill over 30% of the deliveries within one week before the MSB’s publication date. Parts shipments are ongoing and over 80% of possible AOG cases have been avoided.
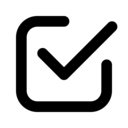
Proactive customer communication
Additionally, we began informing our fleet operators and end customers a week before the MSB’s publication. With the support of our global sales partners, we set up several webinars to discuss in person the impact of the MSB and how we will solve it, and to answer any questions. Further webinars can be scheduled through any of our sales or service partners.
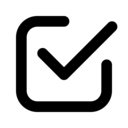
Continuing updates
With the support of our sales partners, we are continuing to keep all our authorized service centers and end customers informed of the current situation and the next steps.
Q & A A few questions answered
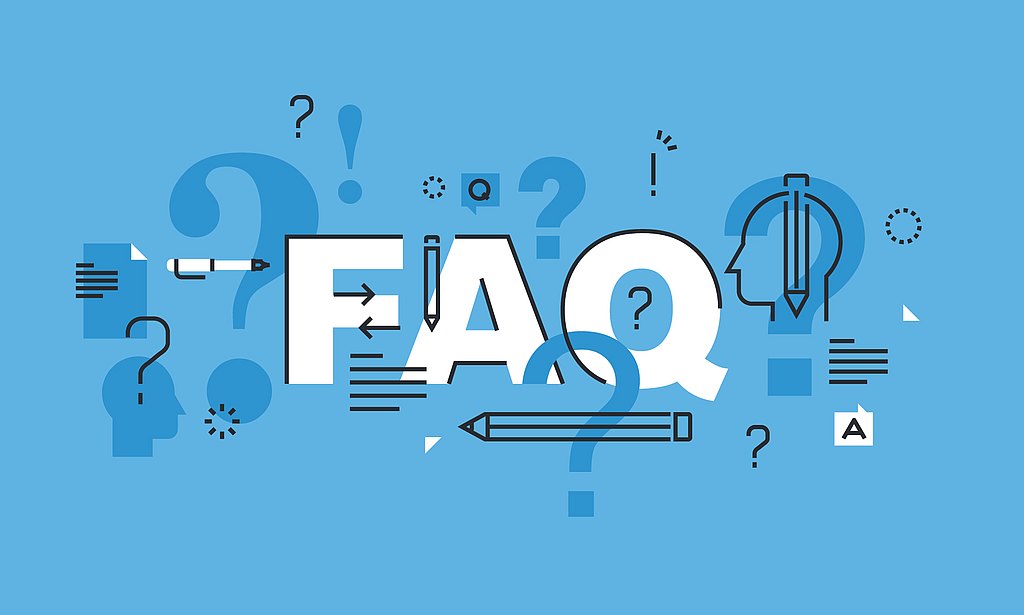
Your Frequently Asked Questions
- Is my aircraft affected? Where can I find my engine registration number?
- What is the financial impact and who will pay for it?
- What is the time impact/downtime?
- Will the authorities issue an emergency Airworthiness Directive (AD)?
If you have any further questions, please contact us
Is my aircraft affected? Where can I find my engine registration number?
- Please contact your service center of choice and enquire about the applicability of this MSB to your plane. If you haven’t been contacted by now, then the chances that you have been affected are very low.
- Engine registration number: please ask your service center to check your engine logbook for more details.
What is the financial impact and who will pay for it?
- Austro Engine guarantees full coverage of material and labour costs during warranty time and beyond.
- Value retention promise: the value of any airplane affected by the MSB will not be influenced. Austro Engine guarantees pro-rated replacement of engines to the owner of the plane up to the original TBR, and this guarantee can be transferred to future owners when reselling the plane. This guarantee has no time limitation.
What is the time impact/downtime?
While the issue lies with a single component, Austro Engine is shipping core engine replacement kits to guarantee a minimum turnaround time. Downtime is expected to be approximately 3 days at our authorized Diamond service centres. Please ask your service center for a binding estimate.
Will there be an emergency Airworthiness Directive (AD) by the authorities?
There are no emergency procedures in place. A regular AD implementing the OEM MSB will be released in due time. Affected engines are therefore safe to fly within the limits set forth by the MSB.
Update 6th December 2022: An EASA AD was released.
Background Austro Engine - From assembling to manufacturing
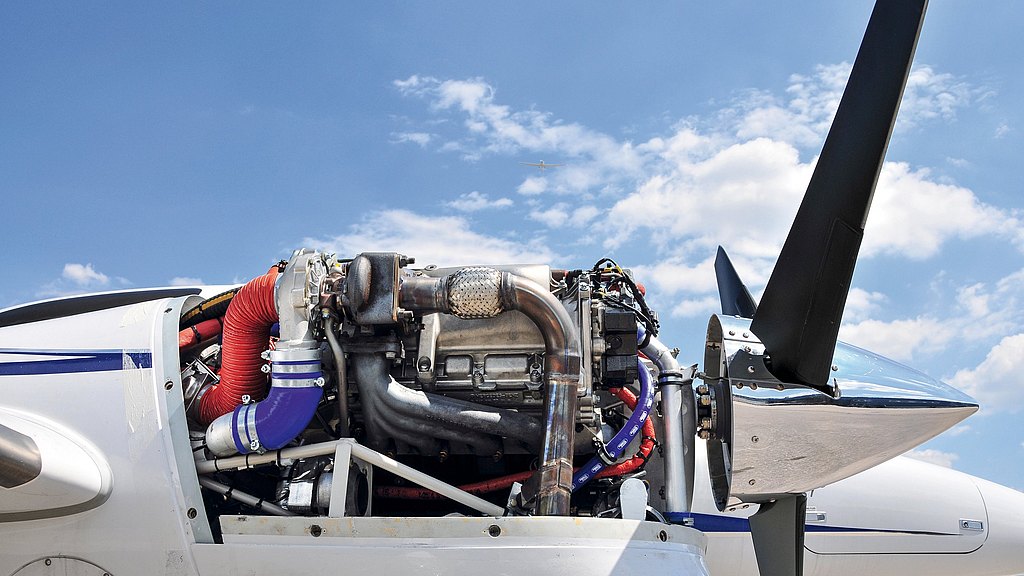
Austro Engine (AE) was founded in 2007 because the former engine supplier for the extremely successful Diamond Aircraft DA40 and DA42 models was not an option anymore and Diamond Aircraft had to find another propulsion solution for its aircraft. In order to remain as compatible as possible and to further provide the advantages of diesel aircraft engines, a similar concept was chosen.
The AUSTRO jet fuel engine is based on a car engine that was further developed and adapted for aviation and finally certified for general aviation. This engine has been used for the Diamond Aircraft DA40, DA42 and DA62 models since 2009. More than 3,000 engines have been delivered and together they have logged more than 2.5 million flight hours. Already at this time, serial production of the car engines by the car engine manufacturer was terminated and a limited batch of the engines was issued to AE. This engine lot was available on stock and called off by AE in line with customer demand and converted into finished aircraft engines.
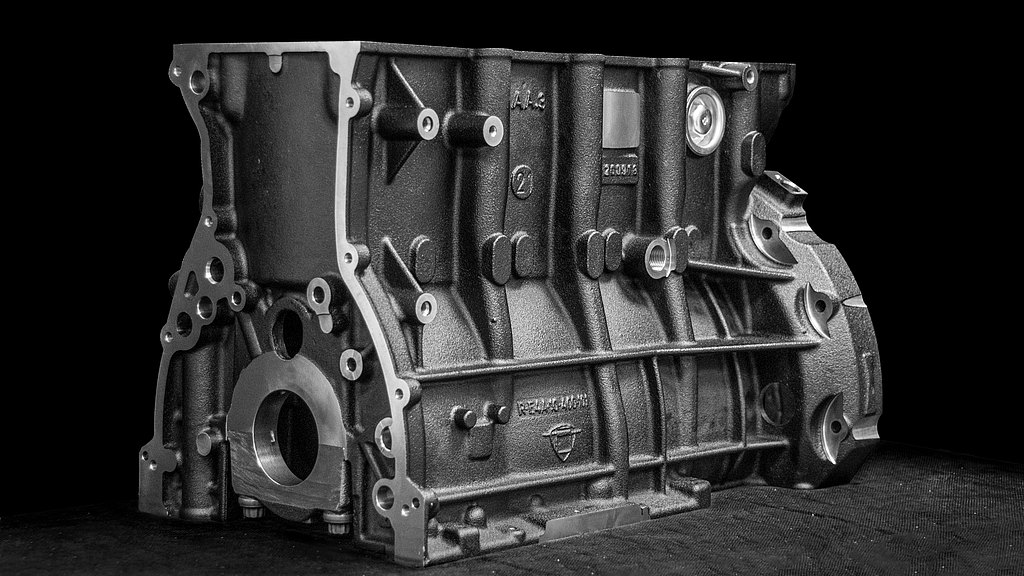
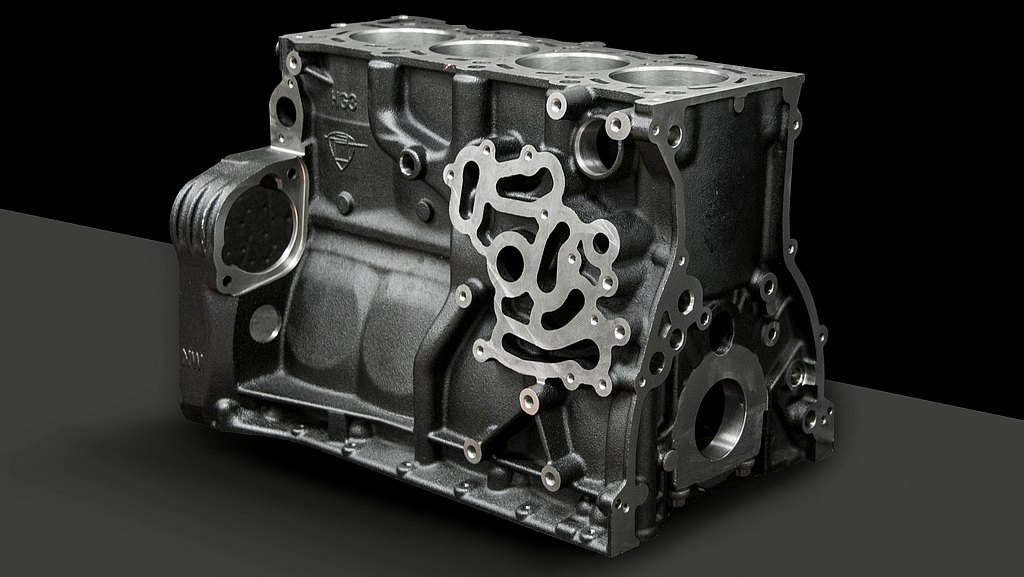
In 2017, AE acquired the right to manufacture these engines under license as a base powerplant for the A4 engines and went from being just the assembler to taking over the engine design and production organization in full. Controlling design elements and manufacturing elements is no trivial tasks and Austro Engine has put in place a resilience plan that helps navigate the transition process. During this transition the company has seen a considerable increase in engine demands that resulted in doubling the engine output from about 400 to about 800 engine units per year. While the fleet of Diamond Aircraft planes keep accumulating flight hours year over year, the safety record for the Diamond fleet, including AE powered aircraft, remains stable at a value of 1 accident per 100.000 hours flown (US NTSB data) over five times lower than the national average in the USA.
This achievement was possible thanks to a series of service bulletins that while addressing incidents from the field took major steps in securing a robust design of the AE product line for the years to come.
Challenges when using automotive technology:
- Wear and tear of material: diesel technology originally applied in the automotive sector (where the ratio of used power to available power is on average well below 50%) is used in the aviation sector where this ratio is much higher. Moreover, jet fuel is more aggressive than diesel fuel to engine components in general.
- Adopting a relatively new technology in a strictly regulated environment like general aviation poses a number of challenges, especially when happening during a relatively short time (3 - 5 years since the license was obtained compared to several decades for other competitors). Therefore, the frequency at which service bulletins are issued is higher. Nevertheless, an analysis of the matters addressed in the SB’s shows that the issues are common across the spectrum of engine providers in the market today.
- Low volume supply chain: as the automotive industry is moving towards electrification and countries in which diesel engines are widely used (like in Germany) begin to transition to renewable energy sources, the availability of components that traditionally were produced in millions of units is at risk. When a supplier has to keep producing low volume of components that are no longer needed by the big car companies it is easy to understand that the availability of reliable suppliers able to deliver quality over a long time is decreasing. Fewer suppliers means that contingency plans in case of disruptions are very hard to put in place.
Contact You have further questions?
Couldn’t find the information you were looking for or do have any further questions? We are there for you.
Partner Portal
As a service center or fleet customer you can get in touch with us via our Partner Portal